What Is a Solar Cell?
Table of contents
- What Are Solar Cells?
- How Does a Solar Cell Work?
- How Are Solar Cells Made?
- Types of Solar Cells
- Frequently Asked Questions
- Final Thoughts
Solar cells are the tiny but essential building blocks of every system that generates electricity by harnessing the renewable power of sunlight.
Photovoltaic modules — such as solar panels — may contain hundreds of solar cells, but even the smallest solar-powered device must have at least one to function.
Most commercial solar cells are made primarily from one of the most abundant materials on Earth, but the manufacturing process is far from simple.
If you’re wondering how solar panels produce electricity from sunlight, there’s no better place to start than by understanding the fundamentals of solar cells and how they work.
Let’s dig in.
What Are Solar Cells?
All renewable energy systems that generate electricity from sunlight use the photovoltaic effect to transform photon energy from solar radiation into direct current (DC) power.
Photovoltaic (PV) cells — more commonly known as solar cells — comprise the semiconductive material that enables solar panels and other PV modules to generate electricity.
PV modules come in many shapes, sizes, and rated power outputs, but they all rely on solar cells to function.
Over 90% of solar panels currently deployed worldwide use crystalline silicon as the primary material in solar cells.
Other types of solar cells — such as thin film — exist but are typically only used in specialised utility-scale applications due to their much lower efficiency rating.
Let’s explore how crystalline silicon solar cells generate electricity from visible light.
How Does a Solar Cell Work?
Solar cells are the fundamental component of photovoltaic modules that generate electricity from sunlight.
Solar panels can be rigid, flexible, or portable, but they all rely on PV cells housed in a protective covering — often an aluminium or stainless steel frame covered by tempered glass.
Even low-wattage applications — like solar-powered calculators — rely on PV cells.
A single solar panel typically has over 100 PV cells, and even smaller modules, like solar shingles, contain between 4 and 12 small cells.
Most solar cells are made from silicon, a naturally semiconductive material that’s extensively processed to produce the photovoltaic effect and maximise efficiency and performance.
The photovoltaic effect captures photons from the solar spectrum — electromagnetic radiation from the sun that reaches Earth as light or heat.
The solar spectrum includes ultraviolet (UV), visible light, and infrared (IR) radiation.
Solar cells are designed to absorb photons with sufficient energy to free up electrons in the semiconductor material (silicon), creating direct current electricity.
Visible light typically generates the most electricity, but UV and some portions of the near-infrared spectrum also contribute to the photovoltaic effect.
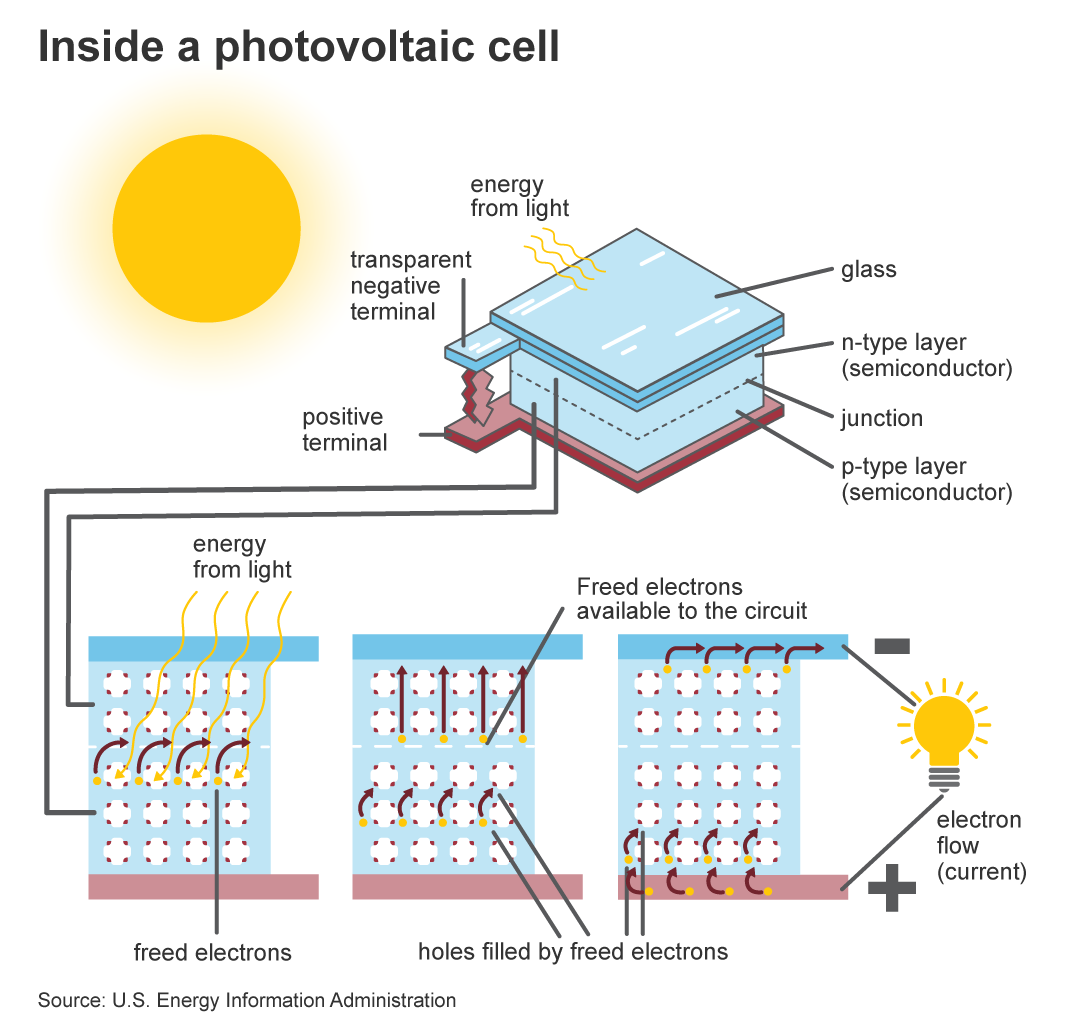
Solar Cell Structure
Semiconductors are an essential building block in nearly all modern electronics, including mobile phones, microwave ovens, computers — and solar panels.
Most solar cells use monocrystalline or polycrystalline silicon as the primary semiconductive material.
The silicon is treated with a process called doping, which intentionally introduces impurities to create positive (p-type) and negative (n-type) layers of semiconductive materials.
The p-type and n-type silicon layers form a p-n junction, essential for converting photon energy to direct current using the photovoltaic effect.
A p-n junction is an essential, but not the only, part of photovoltaic cells.
Here’s a summary of the typical components that make up the structure of silicon solar cells.
- P-type and n-type silicon (to form the p-n junction)
- Front contact (Grid) to capture electrons
- Anti-reflective coating (ARC) to maximise absorption of light
- Back Surface Field (BSF)* used in PERC and other PV cell designs to increase efficiency
- Rear Contact to complete the electrical circuit, typically, an aluminium layer that covers the entire back surface of the cell
- Transparent Encapsulant (usually EVA) to protect the interior of the PV cell and aid in bonding to the module's transparent surface and rear panel.
- Passivation Layer* (often silicon dioxide or silicon nitride) applied to the silicon surface to improve PV cell efficiency. *Optional
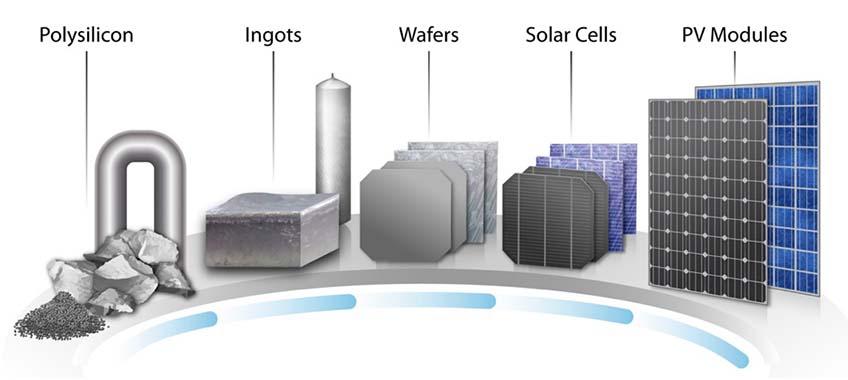
(Source: NREL)
How Are Solar Cells Made?
The vast majority of PV modules — particularly solar panels for residential use — use crystalline silicon as the primary photovoltaic material.
There are other options — such as thin film solar cells — but here we’ll focus on the manufacturing process behind pure monocrystalline and polycrystalline PV cells.
Here’s the journey from sand to solar panel, step-by-step.
1. Mining Raw Materials
Quartz sand is one of the most abundant materials on the Earth’s surface. It is indispensable in many applications, including glass making, construction, and solar cell manufacturing.
Quartz sand is typically extracted from the Earth through open-pit surface mining, although undersea dredging is sometimes used.
Careful management of mining and dredging is required to minimise the environmental impact of quartz extraction.
Quartz’s natural abundance helps keep silicon solar cell prices low, as far more money is spent on processing than acquiring the required raw materials.
2. Silicon Purification
Once the raw mined quartz sand is extracted, the lengthy purification process begins.
First, the sand is washed and screened. Magnetic separation removes iron, and additional processes, like acid leaching, eliminate undesirable impurities.
The upgraded quartz sand is suitable for conversion to Metallurgical-Grade Silicon (MGS), through a chemical reduction process, when combined with carbon in an electric arc furnace at extremely high temperatures.
The resulting MGS is about 98% pure — not pure enough for solar cells or precision electronics such as semiconductors and microchips.
Two different purification processes are commonly used to produce Electronic Grade Silicon (EGS), which must be at least 99.9999% pure.
First, the MGS is converted into silane.
Next, the purified silane gas is decomposed at high temperatures to produce high-purity silicon.
This silicon is then further processed into high-purity polysilicon using the Siemens Process or the Fluidised Bed Reactor process, resulting in EGS polycrystalline silicon.
3. Solar Wafer Production
The process used to create silicon wafers — the essential component for producing the photovoltaic effect in solar cells — differs significantly based on whether the goal is to manufacture pure monocrystalline or polycrystalline PV cells.
Monocrystalline: The Czochralski (CZ) method is used to “grow” a single crystal of pure silicon by melting EGS in a crucible. A seed crystal pulls molten silicon from the crucible to form a large single-crystal silicon ingot. The ingot is sliced into thin wafers of monocrystalline silicon.
Polycrystalline: Directional Solidification (DS) or Casting is used to create a block composed of many silicon grains. Once again, the EGS is melted in a crucible, but allowed to solidify directionally from the bottom up. This process forms a multi-crystalline ingot composed of many silicon crystals, avoiding the steps required to grow a single, large monocrystalline ingot.
Creating polycrystalline solar wafers is quicker and causes less waste, which typically translates to lower PV module costs.
However, polycrystalline solar panels are typically inferior in efficiency and performance compared to monocrystalline PV modules.
Silicon wafers are cut very thin (approximately 150-200 micrometres), typically using wire saws coated with an abrasive slurry, which results in high throughput and minimal waste.
The wafers are then cleaned to remove contamination, and texturing is often used to reduce light reflection.
4. Doping
Doping is an essential step in the solar cell production process.
Exposing silicon wafers to a dopant gas at high temperatures enables the creation of the positive (p-type) and negative (n-type) layers of semiconductive material required to produce the photovoltaic effect.
Typically, one side of the wafer is doped with boron (p-type) and the other with phosphorus (n-type), forming the p-n junction required to generate electricity from photons and electrons.
5. Metallisation
Silver paste is screen printed onto the front of the wafer, and aluminium to the rear. Electrical contact with the silicon is solidified after firing the metallised wafer at high temperatures.
6. Anti-Reflection Coating (ARC)
A thin coating of anti-reflective material (e.g., silicon nitride) is applied to the wafer's front surface to reduce the reflection of sunlight from the solar cell.
7. Etching (Edge Isolation)
Some solar cells undergo etching or laser ablation to improve electrical efficiency and prevent short circuits.
8. Testing and Sorting
The finished cells are tested to measure electrical performance using voltage, current, rated power, fill factor and other metrics.
PV cell performance is measured in a laboratory using Standard Test Conditions.
Cells are sorted into performance bins based on the test results, particularly maximum power output (Pmax).
Sorting ensures that cells with similar characteristics are combined into PV modules, optimising overall performance.
9. PV Module Assembly
With the manufacturing and testing of the solar cells complete, the individual cells are ready to be assembled into a finished solar panel or a specialised type of PV module, such as a solar tile or shingle.
Most residential photovoltaic rooftop installations use rigid mountable solar panels, with solar cells encapsulated between a transparent front sheet (often tempered glass) and a durable backsheet, and then encased within an aluminum frame.
The number of PV cells in an individual panel varies significantly depending on the rated power wattage and other factors.
For example, 400W rigid solar panels commonly have a configuration of either 108 or 144 PV cells.
The combined power of the solar cells is output from a single connector on the PV modules’ exterior, which can be connected in series or parallel to other panels in the array or to a solar inverter or charge controller.
In grid-tied systems without storage, the array is connected directly to a solar inverter for immediate use or transmission to the National Grid under the Smart Export Guarantee (SEG).
In hybrid PV systems with storage, such as the EcoFlow Home Battery, power from the array is routed first to the solar charge controller and then to the inverter for household consumption.
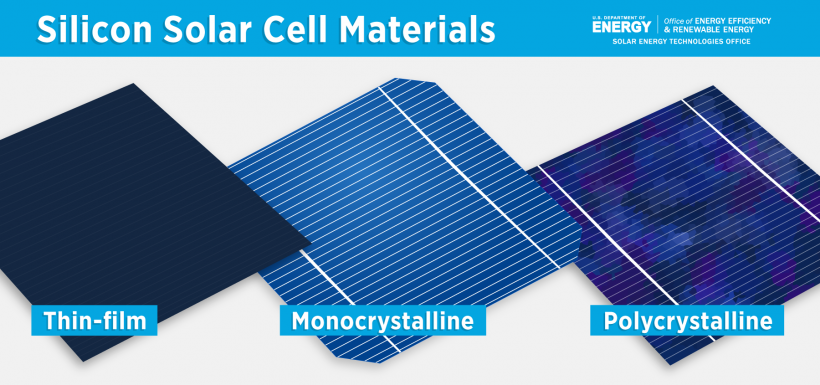
(Source: DoE)
Types of Solar Cells
The type of solar cells in a PV module is the most significant factor in achieving efficiency and performance.
As a result, solar panels and other modules are typically categorized by the type of PV cells used to produce the photovoltaic effect and generate electricity from sunlight.
Other factors, such as module design and manufacturing quality, also play a crucial role, but cell type is the primary driver of performance.
Manufacturers use standardised testing to objectively compare the performance of different solar cell technologies.
All reputable manufacturers use the same laboratory test conditions to test the performance specifications of their solar panels.
Standard Test Conditions for Solar Panels
Condition Type | Standard Test Condition | Real-World Conditions |
---|---|---|
Solar Incident Angle | Always zero, irradiation beam always normal to the PV panel* | Variable, and depends on time, date, and site latitude. In the case of rooftop systems, roof orienta |
Solar Irradiation | Always equal to 1000 Watts/m²* | Variable and depends on the time, date, and site latitude. Limited sunshine hours bound system capac |
Ambient Temperature | Always 25°C* | Variable and depends on the time, date, weather condition, and site latitude. Higher ambient tempera |
Air Mass Coefficient (AM) | Always equal to 1.5* | Variable and depends on the time, date, and site latitude. Higher AM with higher latitudes. |
System Losses (e.g., Wiring, Inverter) | Always Zero* | Variable and depends on the design and location of PV panels, inverter, and grid meter. |
*Cannot be achieved in real-world operation (Source: ResearchGate)
The Standard Test Conditions (STCs) simulate a level of solar irradiation that approximates peak sunlight and other ideal conditions, not all of which can be achieved in the real world.
For example, there’s no such thing as a 100% efficient electrical system, and some power will always be lost when transmitted to the inverter or solar charge controller through wiring or cables.
Regardless, the STCs help consumers compare apples to apples before purchasing solar panels or other PV modules by ensuring the same conditions are used industry-wide amongst reputable suppliers.
The key specs that STCs determine include:
- Rated power: Maximum power output in watts
- Efficiency rating: Amount of direct sunlight converted to DC electricity per square meter of photovoltaic material (as a percentage).
- Open-Circuit Voltage (Voc): Voltage across the cell when no current is flowing
- Short-Circuit Current (Isc): Current flowing through the cell at zero voltage
- Maximum Power Point (Pmax)
Efficiency rating is a crucial spec to focus on when evaluating the types of solar panels and PV cells.
Solar cell efficiency largely determines the size and weight of PV modules, as well as the installation surface area, cost, and number of solar panels required to achieve your electricity generation goals.
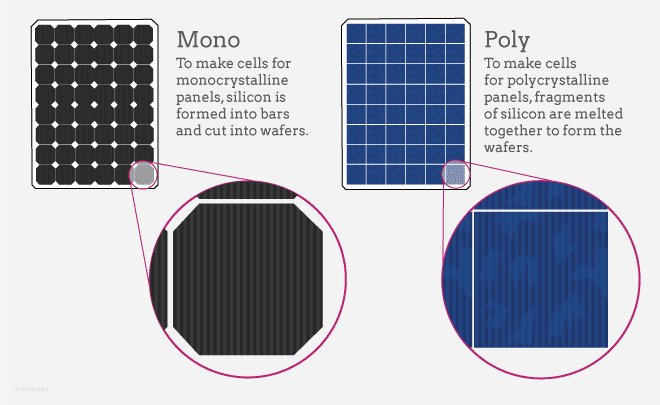
(Source: ASES)
Monocrystalline
Monocrystalline solar cells have the highest efficiency rating, currently topping out at +/- 25% for consumer-grade PV modules.
Higher efficiency typically comes with a higher price tag…
Monocrystalline solar panels tend to be more expensive to produce than polycrystalline due to greater raw material requirements and processing costs.
However, the increased electricity generation from monocrystalline solar cells in many locations outweighs the higher upfront costs.
On average, solar panels last 25-30 years before needing to be replaced.
Once you achieve solar payback — meaning your energy bill savings have outweighed your initial system costs — increased electricity generation can lead to a better return on your solar investment.
This is particularly true if you install solar battery storage and a home energy management system to maximise self-consumption and take advantage of dynamic tariffs and time-of-use rates.
Polycrystalline
Polycrystalline solar cells are cheaper to produce and typically have a lower retail price than PV modules that utilise high-efficiency monocrystalline cells.
However, with average efficiency ratings between 15-18%, any upfront savings will likely be exceeded by the mid-to-long-term opportunity costs of generating less electricity from your available installation area and peak sunlight.
Carefully evaluate how many solar panels are needed to power your house, taking into account how much more electricity high-efficiency monocrystalline solar cells can generate over time compared to your initial investment.
Thin Film
Thin film solar cells do not use crystalline silicon semiconductors to produce the photovoltaic effect.
Instead, thin film PV cells are made from a variety of materials, including amorphous silicon (a-Si), cadmium telluride (CdTe), copper indium gallium selenide (CIGS), and gallium arsenide (GaAs), which are deposited in thin layers onto a substrate such as glass, flexible plastic, or stainless steel.
Most thin film cells are far less efficient than mono or polycrystalline silicon and are rarely used in residential photovoltaic systems.
For example, amorphous silicon (a-Si) cells have an average efficiency rating of 8%-10%.
Cadmium Telluride (CdTe) thin film cells can approach the efficiency of polycrystalline cells in laboratory conditions, but at a higher cost.
It’s essential to note that the performance of solar cells in a lab does not necessarily equate to real-world performance in a commercially available PV module.
Research into thin-film solar cells — and many other emerging PV technologies — continues…
But currently, thin film solar cells are most frequently used in utility-scale installations or specialised applications that require lightweight or flexible panels.
It’s unlikely you would install thin film solar panels at home.
Emerging Technologies for PV Cells
The quest to develop more efficient and cost-effective solar cells is ongoing, and many emerging technologies have shown initial promise.
However, the manufacturing and supply chain for crystalline silicon solar cells is extremely well-established, making it challenging for new technologies to compete on cost and scale.
At least in the short to mid-term, that’s unlikely to change.
Here is a list of emerging PV technologies, mainly in the research and development stage.
- Perovskite
- Dye-Sensitized
- Quantum Dot
- Organic
- Multijunction (III-V)
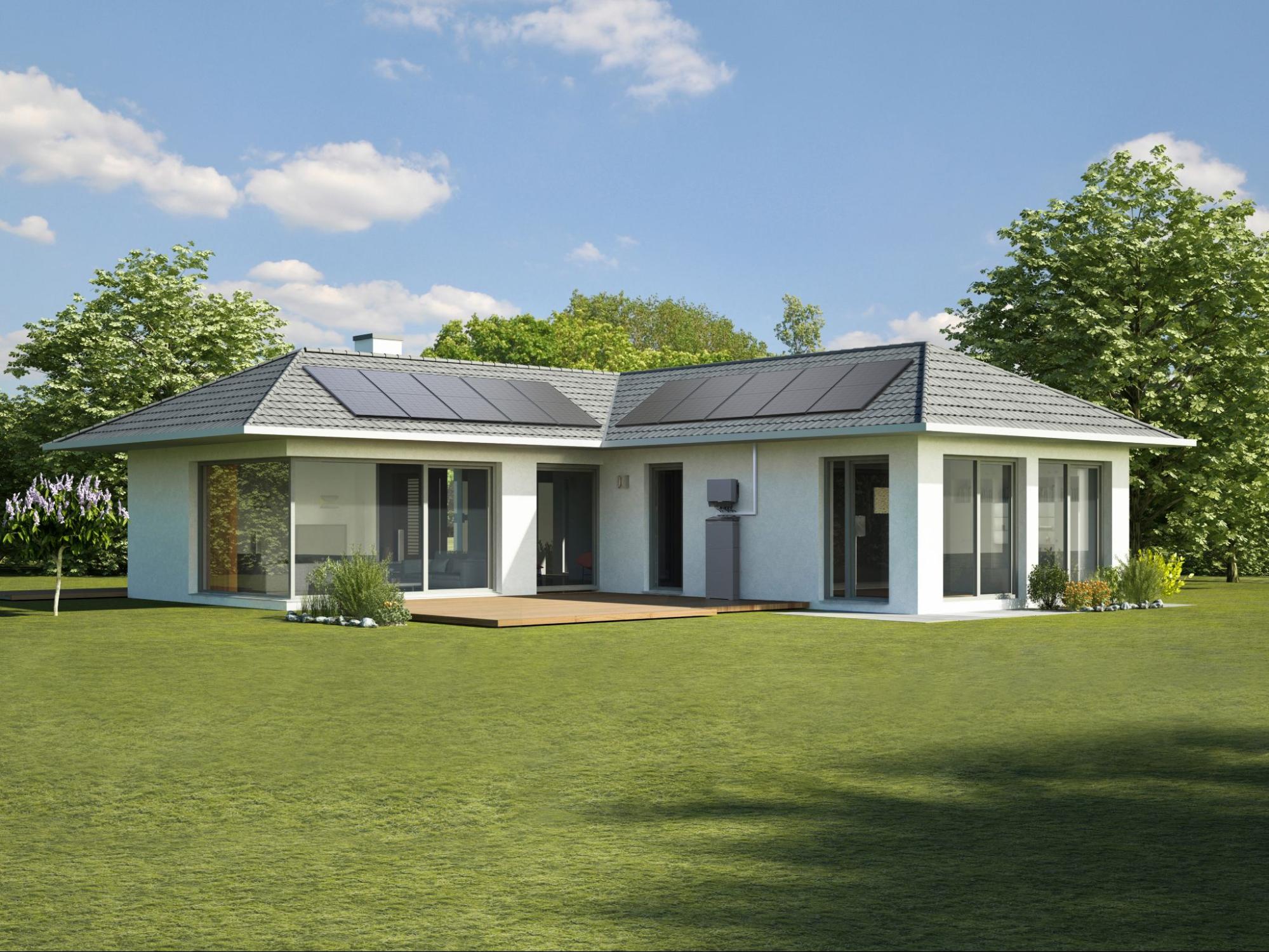
Frequently Asked Questions
Are Solar Cells the Same as Solar Panels?
No. Solar cells are the fundamental component that generates direct current (DC) electricity from sunlight via the photovoltaic (PV) effect, which g. A solar panel is a complete PV module containing multiple interconnected solar cells and protective materials (like tempered glass and a metal frame). It delivers DC power ready for conversion by an inverter into alternating current (AC) for immediate use or storage in a solar battery as DC power.
What Is the Efficiency of Solar Cells?
Solar cell efficiency measures a solar cell's or panel's maximum power output under ideal laboratory conditions (Standard Test Conditions: 25°C, 1000W/m² sunlight). It indicates how effectively the photovoltaic material converts sunlight into electricity. For solar panels, efficiency represents the percentage of the sun’s energy converted per square meter. Higher efficiency means more electricity generation from the same surface area, reducing overall system costs.
Are Solar Cells Worth It?
Solar cells are essential for solar panels and other PV modules that generate electricity from sunlight using the photovoltaic effect. Whether residential solar power is a wise investment depends on numerous factors, including peak sun hours at your location, how much you pay for electricity, and your total household consumption and usage patterns. Home solar + storage systems pay off over the mid-to-long term in many parts of the UK.
Final Thoughts
Without photovoltaic cells, transitioning from burning fossil fuels to using renewable solar energy to generate electricity would not be possible.
Utility-scale solar projects in the UK are helping to increase the resilience of the National Grid, reduce reliance on energy imports, and meet net-zero carbon emission goals.
Thanks to falling prices and innovative technology, there’s never been a better time for homeowners to switch to solar to save on electricity bills and ensure home energy security during power cuts.
EcoFlow Home Battery’s AI-powered Home Energy Management Systems, like PowerOcean, can help maximise your return on investment and reduce your family’s dependence on the National Grid.
Check out our residential solar power and home battery solutions today.